Trustworthy Houston Welding Inspection for Conformity and Safety Criteria
Trustworthy Houston Welding Inspection for Conformity and Safety Criteria
Blog Article
A Comprehensive Overview to Comprehending Exactly How Welding Assessment Functions: Techniques, Criteria, and Best Practices for Top Quality Assurance in Steel Fabrication
Understanding the ins and outs of welding evaluation is crucial for maintaining the integrity of metal construction. Various strategies, such as ultrasonic and visual testing, play an essential role in identifying potential problems, while adherence to developed criteria ensures conformity and sturdiness. Implementing finest techniques can dramatically boost quality guarantee procedures. Nevertheless, the landscape of welding assessment is not without its challenges. What complications occur in the field, and just how can these be successfully reduced? Checking out these aspects discloses the deepness of this important self-control.
Relevance of Welding Inspection
Although welding is a vital procedure in different sectors, its integrity straight impacts the safety and performance of frameworks and components. Reliable welding inspection is crucial for recognizing flaws that might endanger the high quality and toughness of welded joints. This process ensures adherence to established standards and requirements, which are crucial for keeping structural integrity and functional reliability.
Welding examination offers multiple objectives, consisting of confirming that the welding process has been carried out correctly, evaluating the top quality of materials made use of, and confirming that the finished product fulfills regulatory and market criteria (Houston Welding Inspection). Through rigorous examination, potential concerns such as porosity, splits, and insufficient blend can be identified early, stopping costly fixings and minimizing security risks
Moreover, constant welding assessments foster self-confidence among stakeholders, including designers, customers, and regulatory bodies, by showing a dedication to top quality assurance. The value of welding inspection can not be overemphasized; it is essential not just for conformity with lawful demands yet additionally for improving the overall efficiency of welded structures. Inevitably, a durable welding assessment program is a proactive measure that safeguards versus failings, ensuring the longevity and integrity of welded elements in their desired applications.
Common Welding Inspection Methods
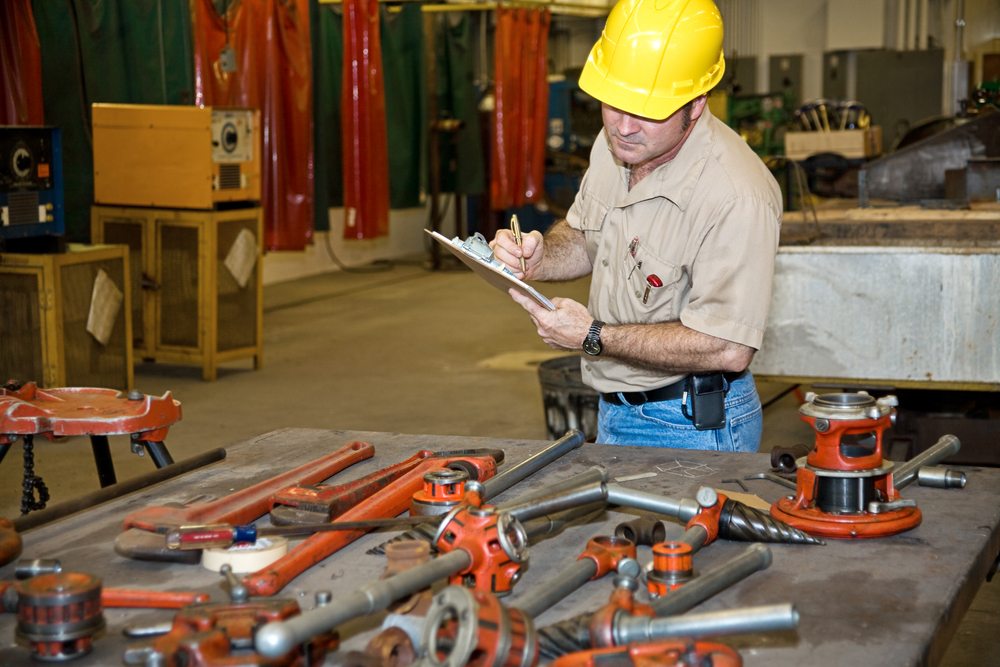
Aesthetic examination is the initial line of protection, enabling inspectors to identify surface problems such as splits, undercuts, or insufficient combination. Radiographic screening utilizes X-rays or gamma rays to reveal inner defects, making it excellent for complex welds. Ultrasonic screening uses high-frequency sound waves to identify subsurface flaws, giving specific dimensions of weld integrity.
Magnetic particle testing is effective for ferromagnetic materials, highlighting surface area and near-surface gaps when particles are related to a magnetic area. Alternatively, color penetrant testing uses a liquid dye to reveal surface-breaking defects, guaranteeing that also the smallest flaws are spotted.
Each technique has its constraints and toughness, usually necessitating a combination of approaches for detailed analysis - Houston Welding Inspection. By applying these examination techniques, quality control in steel construction is accomplished, making certain that bonded frameworks satisfy safety and security and efficiency standards
Sector Specifications for Welding
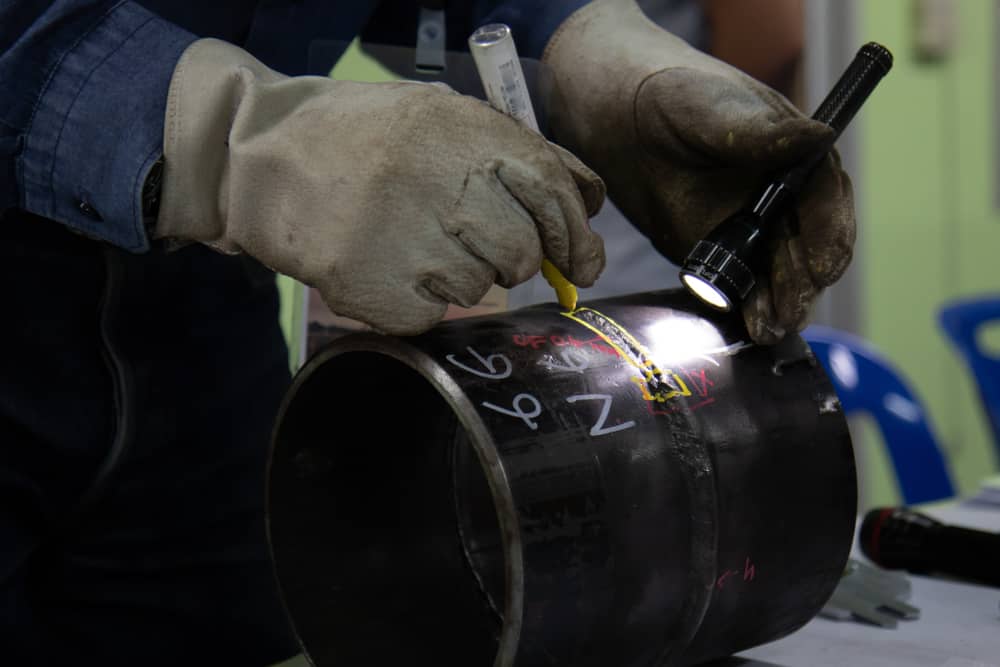

The American Welding Culture (AWS) and the American National Requirement Institute (ANSI) are two noticeable companies that establish welding requirements. AWS D1.1, as an example, outlines the needs for welding steel frameworks, while AWS D1.2 focuses on light weight aluminum. Worldwide, the ISO 3834 standard addresses high quality needs for fusion welding, offering a framework appropriate across national boundaries.

Ideal Practices for Quality Control
Quality assurance in welding is paramount to achieving safe and long lasting buildings. Carrying out best practices makes sure that every weld meets the needed specs and requirements. Establishing a comprehensive top quality administration system (QMS) tailored to the details welding job is crucial. This QMS ought to define functions, treatments, and obligations to mitigate threats and enhance liability.
Regular training and accreditation of welding employees are important for maintaining a competent labor force. Continual education and learning on the most recent welding methods and technologies ensures that examiners and welders are knowledgeable regarding present standards and practices.
In addition, performing pre-weld evaluations to evaluate products and tools can avoid flaws before they happen. Houston Welding Inspection. Throughout the welding process, real-time tracking and documents of welding parameters help recognize disparities immediately. Post-weld inspections must involve comprehensive examinations utilizing non-destructive testing (NDT) methods to make sure the stability of the welds
Furthermore, keeping clear interaction among employee promotes a culture of top quality. Normal audits and reviews of the welding process assistance recognize areas for enhancement. By sticking to these finest techniques, companies can accomplish optimal top quality guarantee, eventually leading to enhanced safety and efficiency in metal fabrication jobs.
Challenges in Welding Evaluation
Although welding examination is vital for guaranteeing structural honesty, it provides a range of difficulties that can complicate the assessment process. One significant difficulty is the variability in welding techniques and products utilized, which can impact the consistency of weld quality. Different welders may employ differing techniques, bring about disparities that inspectors need to evaluate and identify.
Another difficulty includes the detection of issues. Non-destructive screening (NDT) techniques, such as ultrasonic and radiographic testing, can be complicated and require experienced technicians to interpret results properly. False positives or negatives can take place, potentially causing costly rework or compromised safety and security.
In addition, the existence of environmental aspects, such as temperature level and humidity, can influence the stability of welds and the effectiveness of evaluation techniques. Examiners need to likewise browse the regulative landscape, guaranteeing conformity with sector criteria, which can vary by jurisdiction and application.
Verdict
To conclude, welding inspection plays an important duty in guaranteeing the integrity and safety of metal manufacture. Employing a range of evaluation methods, adhering to recognized market requirements, and applying reliable high quality monitoring methods collectively improve the integrity of bonded frameworks. In spite of the challenges faced in the inspection procedure, a commitment to continuous renovation and adherence to finest methods can substantially boost the high quality guarantee structure, cultivating better confidence among stakeholders in the welding sector.
Efficient welding assessment is you could try here necessary for recognizing defects that might jeopardize the top quality and sturdiness of welded joints.Moreover, constant welding examinations foster confidence amongst stakeholders, including engineers, customers, and regulatory bodies, by showing a commitment to high quality guarantee.The American Welding Culture (AWS) and the American National Requirement Institute (ANSI) are 2 noticeable companies that establish welding requirements. Throughout the welding process, real-time tracking and paperwork of welding specifications aid identify disparities right away. In spite of the difficulties faced in the evaluation process, discover this info here a dedication to continuous renovation and adherence to ideal methods can considerably boost the high quality assurance structure, promoting greater confidence among stakeholders in the welding industry.
Report this page